Testing Method
- oliveraa4
- Jan 30, 2019
- 4 min read
Updated: May 13, 2019
Testing Method: Introduction
In this testing procedure, the spring force will be tested on the Composite Recycler. The springs are located on the spring pins that are attached to the shaft guide, which have the shafts attached to them, allowing the shafts to move up and down on the material when in contact, while putting force on the material. The springs should have enough force to put down on the materials so that the cutter won’t pull the composites through, but will instead be controlled. In order to test for this, gauges will be used to see what force of springs will be needed for no slippage, the gauge will be put at an end of the composite to see at what force the springs slips, and multiple springs with different compression forces will be ordered and put on the spring pins and will be ran with composites to test the pull the cutter will have on the material being fed into the recycler. The sheet metal guards will have been put up to provide safety for users.
Method / Approach:
· Acquire different pairs of springs with different compression forces.
· Apply pair onto Recycler.
· Feed composite material.
· Observe how the material gets pulled in comparison to what the handle is being turned.
· Decide which spring forces show best control over feed.
· Acquire spring gauges.
· Use drill to drill hole in composites.
· Create data sheets to insert values gathered
Test Modifications:
There were modifications made for the week of 2/18/19 – 2/24/19. For the first test that will be done will be on the spring forces and determining how much spring force that will be needed in order to press down on the composites so that the material doesn't just rip through with the cutter. In order to test this, 2 springs at a time will be ordered, all with different compression forces to test which one puts enough force on the composites while not stopping to the rest of the process from happening. In other words, it'll be trial and error until a force works with the shaft guides and spring pins in corresponding to the shaft.
Tests were ran on 4/8/19. There weren't any testing issues when doing the three first tests that were done on the frame. There also weren't any modifications due to the testing plan being followed and met by the tests. The tests were meant to determine the initial spring rate and spring pressure on the existing springs on the frame. The tests also help figure out the resistance that would be needed for the composites not to slip. Composites were also fed into all shafts with spring pressure on the shafts and there was a device attached to pull and measure the spring rate the springs have.
Test were ran on 4/22/19. For the second set of testing, springs were ordered with different spring rates from the original set of springs. These springs varied in strength but were stronger than the original springs placed onto the Recycler. The top plate was removed, then the original springs were removed and replaced by the first set of springs. The top plate was then closed and the composite material was placed through the shafts. Then a spring gauge was attached to the composite material and force was pulled in an increasing fashion until the material started to slip from the force, then the pounds were recorded. Then the process was repeated three more times with the same springs to gain an average slippage. Then the top plate was removed again and the springs were swapped out to the second set of new springs where the same process was done to gather another three samples of data. The springs both showed big improvements from the existing springs because they were able to withstand more pounds in the horizontal side, where the existing cutter will do the same, pull the composite material. For the smaller springs, the material slipped between 55-58 pounds. For the bigger springs, the material slipped between 52-54 pounds.
Test Procedures:
Test 1: Required Spring Force for no Slippage.
1. Detach top plate.
2. Remove springs.
3. Use two spring gauges and place them where springs would go.
4. Insert composite material.
5. Push down on spring gauges while person is attempting to pull out the material and figure the force needed and produced on the spring.
6. Repeat steps 3-5 two more times.
Test 2: Existing Spring Resistance
1. Acquire new composite material.
2. Drill hole towards the end of the composite material.
3. Attach spring gage to end where hole is located.
4. Insert material through all 3 rollers.
5. Pull on the material until slipping starts.
6. Record the pounds.
7. Repeat steps 1-6 two more times.
Test 3: Existing Spring Rate (Original)
1. Take springs off Recycler
2. Put springs stacked on compression tester
3. Acquire 3 compression lengths with pound-force
4. Calculate spring rate using spring rate equation.
Test 4: Which Springs Best Fit
1. Get multiple pairs of springs with different compression.
2. Detach the top plate.
3. Place first pair of springs on spring pins.
4. Bolt down the top plate.
5. Turn on Recycler.
6. Feed material into Recycler.
7. Record observations, time, and distance material moved.
8. Repeat Steps 2-7 with different pair of springs.
9. Decide which springs work the best while having no slippage of the materials.
Tests:
Test One: Spring Gauge Test: Dual Gauge Pulling Down
In this test, two spring gauges were used to replace the springs located on the spring pins. Composite material was then inserted. Both gauges were then pulled downward while the material was being pulled out until a force was acquired that didn’t let the material slip. Then the values were recorded.

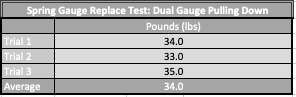
Test Two: Existing Spring Rate
In this test a single spring gauge was used. A hole was drilled at the end of the composite material. The spring gauge was then attached. The material was inserted through all 3 rollers. Then the gauge was pulled and the resistance was recorded when slipped.
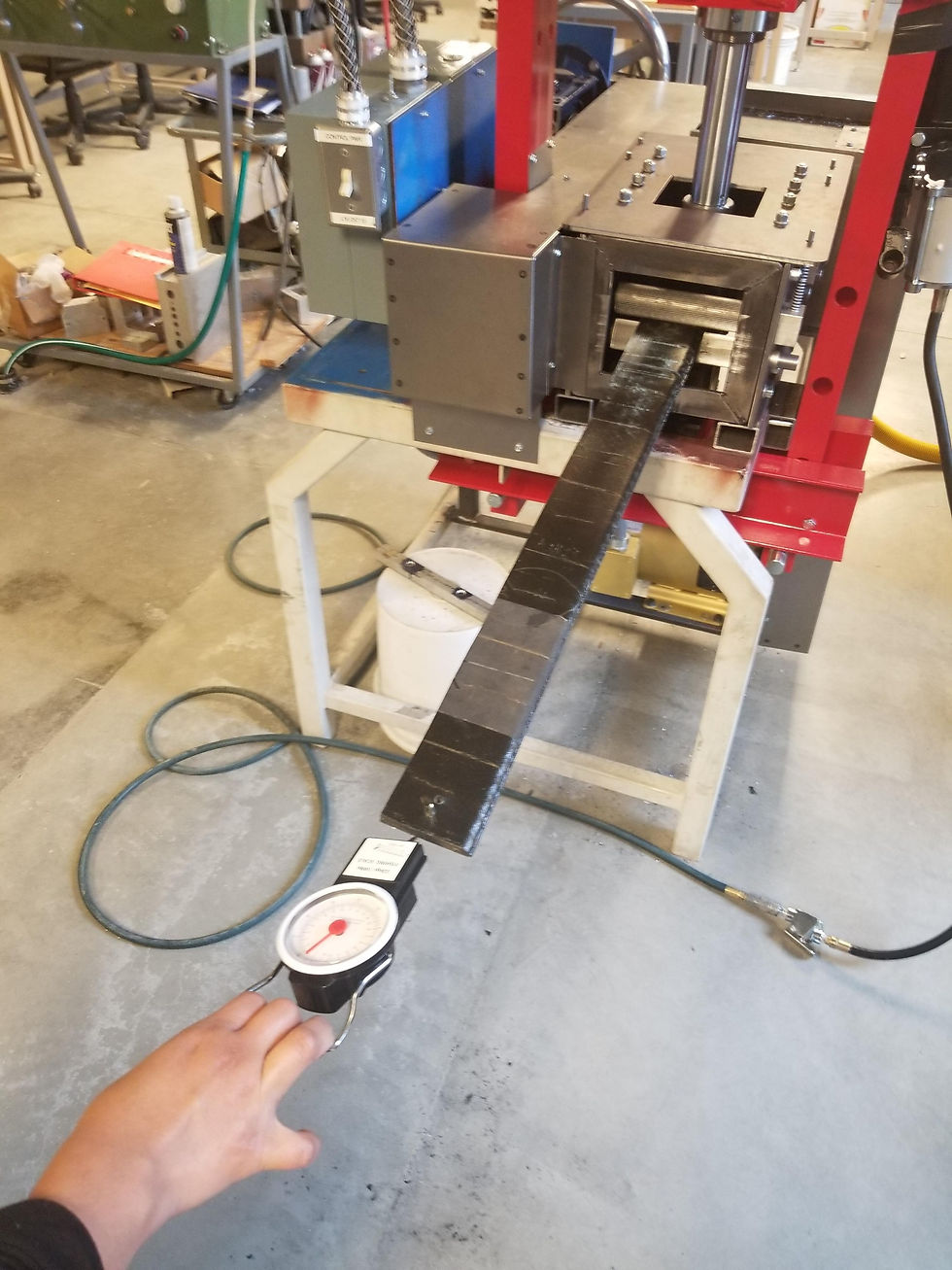
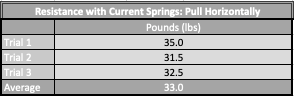
Test Three: Spring Rate
In this test the compression tester was used. The springs were stacked on top of each other as they are on the frame. Then the springs were compressed at three different lengths and the pound-forces was recorded. Then the spring rate was calculated.
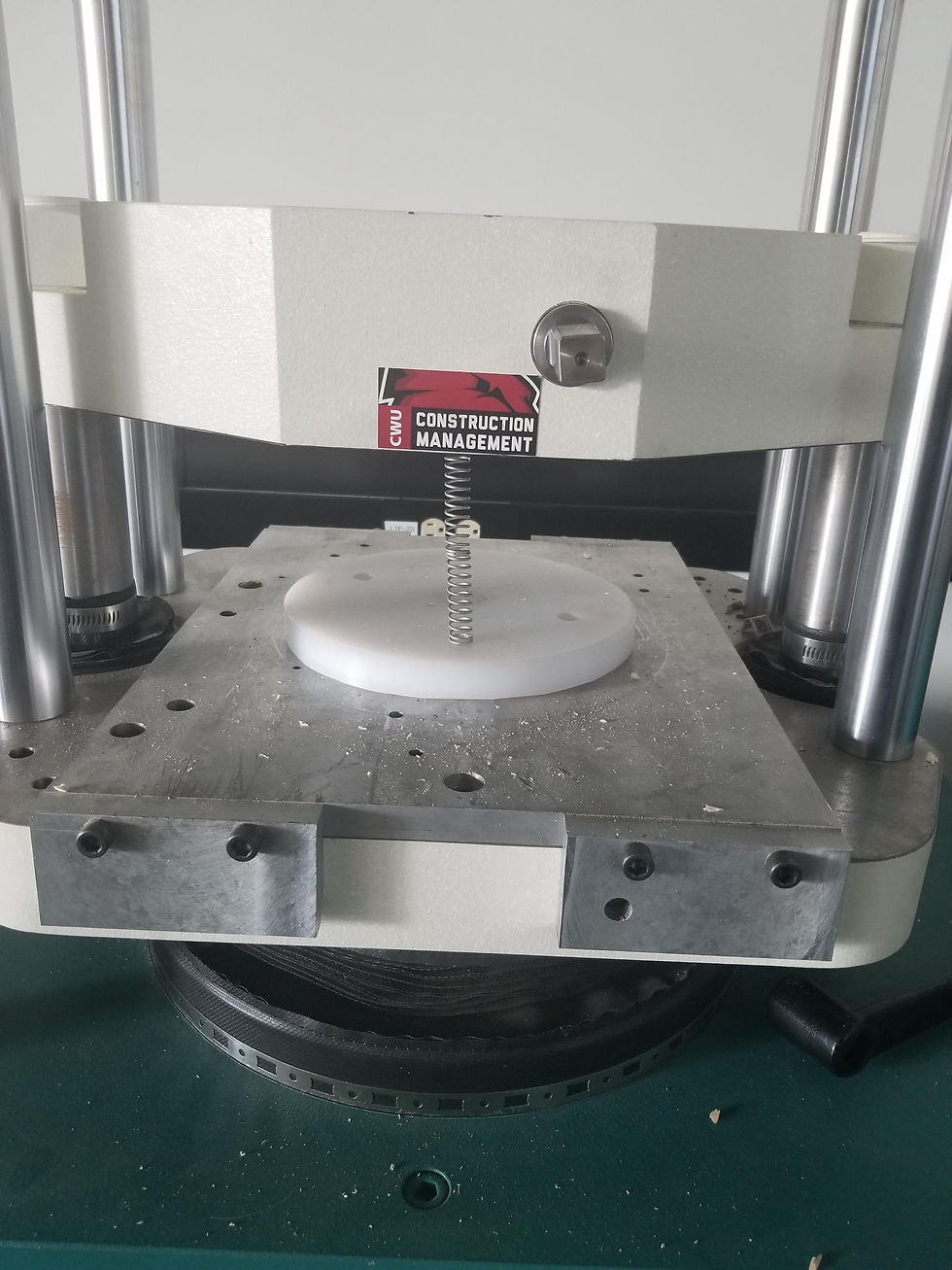
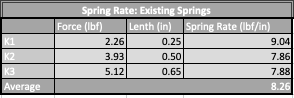
Test Four: Which Springs Best Fit
In this test, different springs with different spring rates were ordered. They were attached to the Composite Recycler and a pulling test was done with the composite material and the spring gauge.
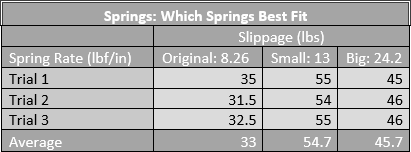
Comments